Choosing a Custom Plastic Enclosures for Electronics is a strategic step in designing an electronic device. Far more than a simple housing, it determines the protection, reliability, ergonomics and perceived value of your product. Between standard enclosures, configurable pre-designed enclosures and fully custom solutions, how do you make the right choice? This practical guide helps you define your priorities and find the most suitable solution.
STANDARD, CONFIGURABLE OR FULLY CUSTOM PLASTIC ENCLOSURES?
5 key questions to ask yourself before deciding:
Before selecting your enclosure, take time to evaluate your constraints. These five essential questions will help you clarify your requirements:
- What mechanical and environmental constraints?
Does your enclosure need to withstand heat, impacts, humidity, UV or chemicals? - Is your electronic design fixed or likely to evolve?
If your design may change (adding connectors, updating the PCB), favour a flexible solution. - What aesthetic and functional requirements?
Will the enclosure be visible to the end user? Should it incorporate transparent areas, ventilation or specific fixings? - What are the expected quantities?
Are you producing prototypes, a small batch of a few dozen units, or a recurring production? - What lead times and budget?
Does your project need to be launched quickly? What budget have you planned?
Standard, configurable or custom plastic enclosure ? Understand the differences
In the world of plastic enclosures, you have several options:
Well-known manufacturers such as OKW or Hammond Manufacturing offer ready-to-use enclosures. These models are economical and available from stock. They are ideal for simple projects and very short lead times. However, their dimensions and features are fixed. Adaptations (cut-outs, drilling) often require manual processing or subcontracting, which can affect quality and create additional delays.
Configurable pre-designed enclosures: Electronicase UK Configurator
If your project is too specific for a standard enclosure but not complex enough to justify a fully custom design, you are probably in the grey zone.
In this case, we offer on our website Electronicase: Custom plastic enclosures without tooling costs in 5 days, a simple online configurator available free of charge. You can independently:
- Select from over 40 customisable models.
- Set your cut-outs, drillings and markings in just a few clicks.
- View your project in real-time 3D.
- Receive an instant quote and benefit from short manufacturing times.
At this stage, it is essential to define these 3 points:
Technical: What functions must the enclosure fulfil?
Budget: What economic model is the most appropriate?
Aesthetic: Will the enclosure be visible? What finish do you want?
Example – EC10-200 Multifunction Enclosure:
To illustrate the possibilities offered by our configurator, here is a concrete example:
Model: EC10-200-0 plastic enclosure
Concept: Two U-shaped parts clipped together by tongue and groove
Dimensions: 220 × 130 × 35 mm
Weight: 248 g
Applications: Integration of multiple connections (USB, HDMI, power supply, antennas), top and side ventilation, customised front panel with colour marking.
This example shows that a configurable enclosure can meet demanding technical constraints while maintaining a refined design and controlled lead time.
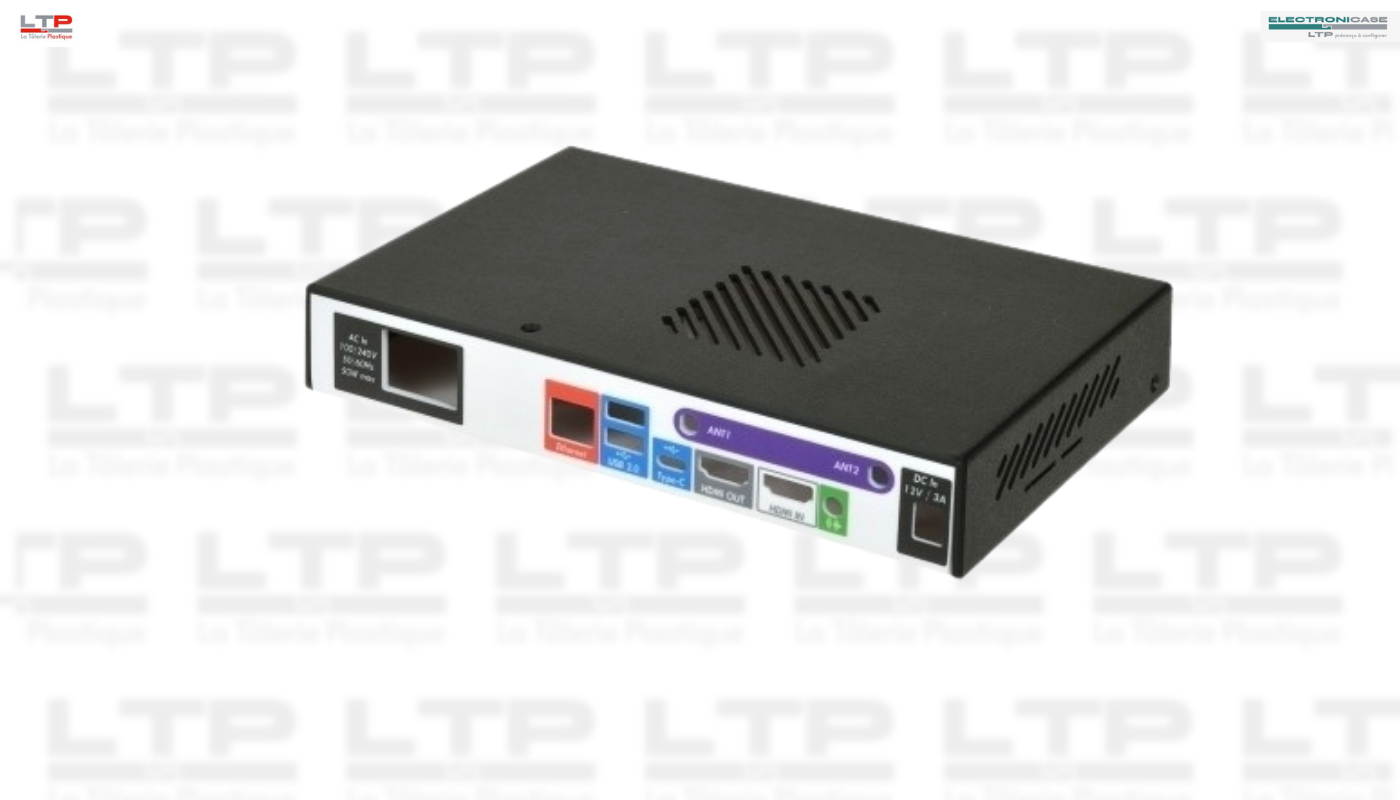
Learn more about our examples: LTP : the alternative to conventional plastics technologies
When to choose a fully custom plastic enclosure ?
A fully custom plastic enclosure becomes essential if:
- Your dimensions exceed market standards.
- You need to integrate specific features (partitions, compartments, cable entries).
You have strict regulatory constraints (IP standards: protection against solids and liquids, UL94 flammability classification, certifications).
- You want a unique and identifiable aesthetic finish.
- You are looking for thermal optimisation or EMC shielding.
Why choose mould-free technology?
The custom mould-free plastic sheet fabrication developed by LTP offers tangible advantages:
- No initial investment in tooling, unlike thermoforming or injection moulding.
- Total design freedom, even for complex geometries.
- Short lead times, from 2 to 8 weeks depending on the project.
- Manufacturing adapted to small and medium series (5 to 5,000 units).
- Possibility to modify the design during the product life cycle.
- Eco-design options to reduce environmental footprint.
- Flame-retardant plastic available on request.
This flexibility makes mould-free custom production particularly suited to industrial, medical and IoT service projects.
Conclusion:
Choosing a plastic enclosure is a strategic issue: it protects your components, enhances your product and ensures compliance.
Whether you choose a standard model, a configurable enclosure via Electronicase or a fully custom solution, take time to assess your technical, aesthetic and economic requirements.
Not sure ?
Contact us we will provide the best solution for your needs: our teams are here to guide you and help you make the right choice.
📞 Phone: +33 (0)2 35 44 95 40
📧 Email: sales@ltp.fr
It’s the enclosure that adapts, not your electronics